Polyvalence de l'imagerie thermique dans l'industrie minière
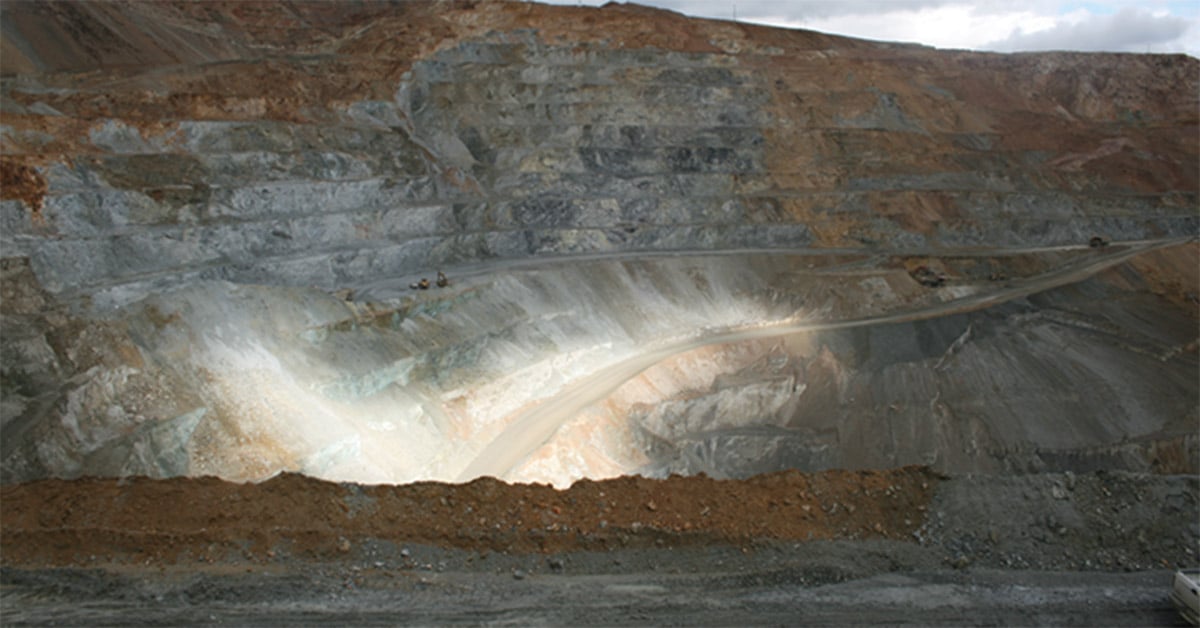
L'infrarouge peut ètre un outil de surveillance essentiel à chaque étape du procédé
RÉSUMÉ
Dans une industrie où les conditions météorologiques et environnementales défavorables sont des normes en milieu de travail pour des centaines de milliers de travailleurs, l’imagerie thermique s’est avérée un outil fiable pour aider à limiter les temps d’arrêt imprévus, améliorer la sécurité au travail et, ce faisant, économiser des millions de dollars. Cette note d’application explore la valeur de l’intégration des imageurs thermiques dans la surveillance de l’état du « procédé » (« procédé » d’extraction du minéral du minerai) et des programmes d’entretien prédictif sur les systèmes électriques et mécaniques dans les opérations minières. Il aborde également les applications plus récentes qui deviennent de plus en plus populaires dans l’industrie minière.
Défi
À bien des égards, un site minier est comme une ville miniature. Il possède ses propres services publics, routes, équipements de traitement spécialisés, normes et réglementations de sécurité ainsi qu’une main-d’œuvre dévouée et qualifiée. Les mines sont exploitées 24 heures sur 24, 365 jours par année. Une vaste infrastructure fournit l’alimentation électrique de sous-stations sur place, déplace l’air réfrigéré profondément sous terre et pompe l’eau pour éviter les inondations. Jusqu’à 400 tonnes de camions de transport, de pelles puissantes (à essence et électriques), de concasseurs, d’usines et d’installations de traitement extraient des métaux précieux ou d’autres matériaux essentiels du minerai de kilomètres de tunnels souterrains ou de centaines d’acres d’exploitation minière à ciel ouvert.
Les mines ont besoin d’une alimentation électrique étendue provenant de sous-stations sur place.
Les coûts des temps d’arrêt
Le potentiel de revenus d’une mine est directement lié à sa production qui est déterminée par le fonctionnement de tous les systèmes sans interruption inattendue. Par exemple, le projet et la future mine Gold Bar estiment un profil de production de 62 800 onces d’or par année. Fonctionnant 365 jours par année, cela veut dire un peu plus de 172 onces par jour et de 7,17 onces par heure. Si le prix de l’or est de 1 200 $ l’once, le revenu horaire perdu en raison des temps d’arrêt est de 8 628 $. À ce taux, il faut moins d’une semaine pour qu’une mine perde un million de dollars. Certaines mines produisent moins et d’autres beaucoup plus, et cet exemple ne tient même pas compte de l’augmentation des coûts d’exploitation qui est également susceptible d’émerger de la panne.
La durabilité et l’entretien de l’équipement comptent pour beaucoup dans les coûts d’exploitation d’une mine. Une grande partie de l’équipement est personnalisée et est si spécialisée que son remplacement est hors de prix. Et les véhicules coûtant jusqu’à des millions de dollars chacun, les sociétés minières doivent utiliser leurs camions, pelles et équipements de lixiviation, de la façon la plus efficace possible.
Défis de la maintenance prédictive dans l’industrie minière
Pour éviter les temps d’arrêt ou les pertes d’équipement catastrophiques et pour réduire les primes d’assurance et améliorer la sécurité des travailleurs, les sociétés minières gèrent des programmes complets de maintenance prédictive pour fournir une alimentation ininterrompue et un temps de fonctionnement continu. La taille de l’opération détermine la taille des équipes qui gèrent les programmes. Mais étant donné la complexité des systèmes électriques et mécaniques des opérations minières, ces équipes ont besoin de connaissances et de formation sur l’équipement minier, le transport et les applications électriques. Bien qu’il soit courant pour les sociétés minières d’impartir certaines tâches, il est plus rentable de garder une grande partie de la surveillance et de la réparation à l’interne. Peu importe qui exécute les tâches de maintenance préventive, l’industrie minière présente certains défis uniques qui doivent être relevés pour réussir, notamment :
- Conditions environnementales : Que ce soit en raison du travail de nuit ou souterrain ou des conditions de chaleur ou de froid extrêmes ou humides, la plupart des mines offrent de nombreux défis uniques à la surveillance et à l’entretien de l’équipement 24 heures sur 24.
- Poussière : L’exploitation minière, par nature, est un travail sale. Mais certaines mines sont pires que d’autres. Par exemple, les mines de charbon souterraines présentent un problème de poussière plus important que les mines de cuivre ou d’or à ciel ouvert.
- Passage au numérique : L’industrie minière tire parti des avantages de la numérisation des opérations. Comme toute industrie, un accès plus rapide aux données améliore la rentabilité et la productivité. Elle a besoin de solutions de surveillance numérique, qui produisent des données qui peuvent éclairer la prise de décision en temps réel, ce qui se traduit par un retour sur le capital investi (RCI) plus rapide.
DOWNLOAD Note Here
Solution
Il y a plus de 20 ans, Per Fostvedt, fondateur d’Infrared Systems d’Ogden, Utah, a commencé à promouvoir l’imagerie thermique aux opérations minières comme moyen d’améliorer les programmes de traitement et maintenance prédictive.
« Lorsque j’ai commencé à visiter les mines, faisant la promotion de l’IR, il y a plus de 20 ans, la réception était surtout négative. Parce qu’à cette époque, la philosophie était de faire fonctionner l’équipement jusqu’à sa défaillance, puis de le réparer ou de le remplacer », a dit M. Fostvedt.
Mais la philosophie a changé au fil des ans. Des programmes de maintenance prédictive réguliers améliorent la sécurité des travailleurs et permettent d’économiser temps et argent. Les caméras d’imagerie thermique sont devenues un outil de maintenance prédictive vital, plus souvent qu’autrement pour les systèmes électriques et mécaniques, mais aussi pour surveiller de nombreuses opérations de traitement et de lixiviation en tas.
La sécurité des travailleurs est une priorité importante pour l’industrie minière. En général, s’il existe une solution qui améliore la sécurité, les sociétés minières sont prêtes à investir.
De nombreuses mines possèdent des caméras et des logiciels d’imagerie thermique et envoient les employés à des cours de formation infrarouge pour qu’ils comprennent mieux les applications et apprennent comment fonctionnent les caméras infrarouges. En fait, et cela illustre comment l’industrie minière perçoit l’importance de l’imagerie thermique depuis que M. Fostvedt a lancé Infrared Systems, trois cours de certification thermographique ont été planifiés et comblés par des sociétés minières en 2018 à Elko, Nevada. En raison du succès obtenu, les sociétés minières du sud-ouest des États-Unis veulent continuer, voire accélérer ce rythme en 2019.
Les sociétés minières emploient également des professionnels externes spécialisés qui doivent être en mesure de recueillir des données d’imagerie thermique de qualité, de prendre des mesures de température précises et de fournir en temps opportun des renseignements sur l’état de l’équipement à l’aide de concepts de transfert de chaleur par thermographie tant qualitative que quantitative. Les entrepreneurs doivent obtenir les certifications appropriées de la Mining Safety and Health Administration (MSHA), suivre une formation sur les dangers et la sécurité sur place et effectuer des vérifications des antécédents. Néanmoins, les professionnels de la thermographie externes fournissent des conseils d’experts basés sur des procédures d’inspection appropriées sur les schémas thermiques identifiables, dont certains peuvent prendre du temps à se manifester.
RCI électrique
Figure 1. Défaillance prochaine d’un régulateur de tension d’une sous-station minière.
Les opérations minières dépendent fortement de l’énergie électrique pour l’extraction, le transport et le traitement du minerai, car elle est plus efficace, économique et écologique que l’énergie diesel. La taille et les niveaux de tension sont généralement plus élevés sur un site minier que dans la plupart des autres industries. En fait, l’exploitation minière s’est classée troisième derrière les industries des produits chimiques et du raffinage en vrac en consommation d’énergie en 2017 selon la U.S. Energy Information Administration.
L’énergie est distribuée dans l’ensemble du site de la mine à partir de sous-stations et passe par des lignes de transmission de haute tension, puis vers des sous- stations mobiles et dans des transformateurs. L’image thermique de la figure 1 montre une terminaison de régulateur de tension de sous-station prête à défaillir. Cette sous-station a alimenté des opérations vitales et, si elle avait défailli et forcé une fermeture imprévue, la perte de revenus aurait pu atteindre des millions de dollars.
Figure 2. Défaillance prochaine d’une terminaison d’entrepreneur qui alimente un moteur de traitement VFD.
Encore une fois, à la figure 2, lors d’une inspection contractuelle sur un autre site minier, M. Fostvedt a découvert une terminaison de contacteur de 480 V dans un compartiment du centre de commande des moteurs (CCM) prête à défaillir. Ce compartiment CCM a alimenté un moteur à variateur de fréquence (VFD) dont la défaillance inattendue aurait pu entraîner une perte de revenus de traitement allant jusqu’à 100 000 $.
RCI mécanique
Selon la Gates Corporation, les temps d’arrêt imprévus sur un site minier entraînent une perte de production pouvant atteindre 180 000 $ par incident. L’une des pièces d’équipement les plus coûteuses pouvant entraîner de telles pertes est la pelle à câbles. Une pelle à câbles est le lien vital de toute exploitation minière. Si elle tombe en panne à l’improviste, les conséquences se propagent dans tout le processus minier. La plupart des sites n’ont pas de pièces de rechange de pelle à portée de main. Selon le problème et l’âge de la pelle, la pièce peut même ne plus être fabriquée.
Figure 3. Le cylindre de flèche gauche de cette pelle à câbles commence à surchauffer en raison d’un manque de graisse.
Le temps d’arrêt peut durer des jours et c’est pourquoi une maintenance régulière, y compris IR, est si importante. En général, un quart de travail de 12 heures par mois est alloué aux applications de maintenance prédictive. Des problèmes, comme la surchauffe des cylindres de flèche (Figure 3) qui peuvent être détectés pendant l’entretien régulier prévu avant le dysfonctionnement, peuvent faire la différence entre une réparation pendant un quart de travail de 12 heures ou la perte de 180 000 $/heure en production et l’achat d’une nouvelle pelle à câbles électrique de 7 200 V coûtant plusieurs millions de dollars.
Autres applications de l’industrie minière
Les applications d’imagerie thermique dans l’industrie minière vont au-delà de la maintenance prédictive électrique et mécanique. Selon le type de mine, les cas d’application suivants peuvent également s’appliquer :
- Surveillance des conditions : Les caméras d’imagerie thermique fixes et sur véhicule fournissent des images et des données en temps réel à une centrale de surveillance qui suit tout des gradients de température aux armoires électriques et à l’appareillage de connexion. Dans les mines passant au numérique, les données de ces images peuvent être analysées au fil du temps pour prédire plus précisément les défaillances, planifier des périodes d’entretien plus courtes et minimiser les temps d’arrêt de production.
- Sécurité : La taille, l’accessibilité et la sûreté sont des facteurs qui peuvent rendre les patrouilles manuelles des périmètres des sites miniers difficiles. Grâce aux configurations des caméras thermiques et couleurs haute définition qui panoramiquent/s’inclinent/zooment, combinées à un réseau, à un logiciel et à des analyses infonuagiques modernes, le centre de commande d’une mine peut surveiller l’ensemble du site à partir d’un seul emplacement.
- Sûreté : En surveillant l'intégrité des murs d'une mine à l'aide de l'imagerie thermique, les sociétés minières ont plus de données sur la stabilité à consulter lorsqu'elles décident s'il est sécuritaire d'envoyer des travailleurs dans une mine.
- Fenêtres IR : De nombreuses opérations minières demandent que le nouvel équipement comprenne des fenêtres IR pour rendre les inspections d’imagerie thermique pus sécuritaires et plus faciles, en particulier pour l’équipement électrique. De nombreuses mines sont également en cours de rénover leur équipement plus ancien avec des fenêtres IR.
- Drones : La surveillance aérienne sans pilote offre une perspective complète des différences de chaleur invisibles dans les systèmes de transmission électrique à partir de l’air et pour les vides du site minier.
Aider les mines à rester productives et sécuritaires
Les sites miniers ont besoin d’équipement robuste. Même si les caméras d’imagerie thermique voient à travers la poussière, l’accumulation de poussière sur l’objectif peut mettre une caméra hors service. Les spécialistes de mise en œuvre de systèmes FLIR comme Infrared Systems utilisent des systèmes de purge d’air permanents pour éliminer la poussière des objectifs des caméras infrarouges fixes. Pour les caméras IR portatives, les thermographes effectuent souvent des inspections avec les caméras dans des sacs en plastique transparents scellés.
Peu importe ce qu’il faut pour accomplir le travail, l’industrie minière a adopté l’imagerie thermique comme un actif de maintenance prédictive fiable. M. Fostvedt a déclaré : « L’IR est un outil essentiel pour surveiller les transformateurs qui alimentent les systèmes d’arrosage, les systèmes de réfrigération, le traitement, les CCM et les sous-stations tant à la surface que sous terre. »
L’imagerie thermique est une technologie différenciatrice qui aide les sociétés minières à faire ce qu’elles doivent pour réussir : elles doivent suivre une veine où qu’elle aille et elles ne savent jamais où un échantillon les mènera.