La GFx320 à sécurité intrinsèque mesure les niveaux de sable dans des séparateurs sous atmosphère explosive
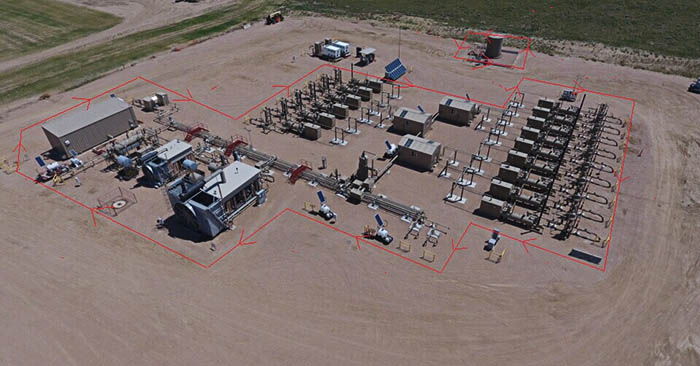
Pendant la fracturation hydraulique, une partie du processus consiste à injecter du sable pour maintenir les pores d'un puits ouverts. Lorsque le puits est remis en ligne après la fracturation, une partie de ce sable remonte à la surface dans un séparateur. Un séparateur est installé à la surface et sépare le pétrole, le gaz et l'eau grâce à la chaleur d'un tube interne. Le gaz est siphonné et acheminé vers un compteur de vente, puis vers les foyers et les entreprises. Le pétrole et l'eau sont recueillis dans des réservoirs sur place puis emportés par des tankers. Les sous-produits indésirables comme la paraffine et le sable s'accumulent dans les réservoirs du séparateur et doivent être éliminés pour éviter des dommages irréparables au niveau du tube chauffant. Si le sable écrase le tube chauffant d'un séparateur sans bride, la seule option consiste à remplacer tout le réservoir. Les séparateurs sans bride composent l'essentiel de l'inventaire de Noble Energy. La réparation et le remplacement d'un tube chauffant ne sont possibles que sur les séparateurs à bride plus récents et plus coûteux.
Des pannes coûteuses et dangereuses
« Ces séparateurs coûtent en moyenne 100 000 $ chacun, » explique Doug Hess, responsable LDAR pour Noble Energy. « Si le sable s'accumule et reste sur l'élément chauffant, il finit par l'écraser, ce qui peut créer une panne catastrophique du séparateur lui-même. Cela peut avoir deux conséquences, toutes deux plutôt néfastes. La première est une fuite de gaz, de pétrole et d'eau hors du séparateur. La deuxième est un incendie. » Les pièges à sable et autres mécanismes de filtrage se sont avérés inefficaces pour maintenir le sable hors des séparateurs. S'il n'est pas possible d'empêcher le sable de rentrer, il faut trouver un moyen de l'éliminer. Le sable et la paraffine sont plus froids que le pétrole, le gaz et l'eau, donc les ingénieurs de Noble Energy passaient la main sur le ventre des réservoirs pour essayer de sentir une différence de température. Cette méthode peu fiable était source de faux négatifs et de faux positifs : des réservoirs endommagés n'étaient pas détectés et des équipes de maintenance étaient mobilisées inutilement.
L'élimination du sable demande des efforts importants
Si l'élimination de la paraffine consiste simplement à chauffer le séparateur et à la traiter avec un produit inhibiteur, l'élimination du sable est une autre aventure. Elle impose l'arrêt total du séparateur et deux équipes d'ouvriers, l'une manipulant des tuyaux et l'autre un camion aspirateur. C'est un processus qui demande beaucoup de main-d'œuvre et, s'il est réalisé inutilement, il se traduit par des pertes de production et d'heures-hommes. Pour éviter le remplacement coûteux des séparateurs dû à l'accumulation de sable et améliorer l'efficacité du programme de maintenance préventive des séparateurs, Noble Energy a élaboré une méthode de mesure du sable qui utilise des caméras d'imagerie optique des gaz à sécurité intrinsèque, les FLIR GFx320.
La solution
Noble Energy utilisait déjà des caméras OGI de FLIR dans son programme de détection et correction des fuites (LDAR). La société avait investi dans ces caméras pour satisfaire la Réglementation 7 du Colorado, Contrôle de l'ozone via les précurseurs de l'ozone et contrôle des hydrocarbures via le pétrole et sous forme d'émissions. Avec plus de 30 000 fuites détectées, les techniciens connaissaient déjà bien le fonctionnement de la caméra. L'équipe a ainsi compris que la technologie permettant de détecter les fuites de gaz invisibles pouvait aussi enrichir le programme de maintenance préventive des séparateurs. « Nous avons cette caméra qui utilise la technologie de l'imagerie thermique et qui est assez puissante pour voir ce qui se passe derrière l'épaisse paroi métallique des séparateurs. En utilisant la différence de température (le pétrole est plus chaud, le sable, plus froid), nous pouvons déterminer s'il y a une accumulation de sable dans les séparateurs, » explique Hess.
La méthode de mesure du sable de Noble Engergy
Il ne faut que quelques minutes pour recueillir des points de température sur chaque réservoir. La palette arc-en-ciel des images thermiques présente des couleurs spécifiques qui varient en fonction de la température (voir figures A et B). « L'arc-en-ciel à fort contraste met en évidence les différences de température de façon optimale et nos techniciens apprécient la plage de visualisation, » explique Landon Hawkins, l'ingénieur responsable du développement de l'essentiel de la méthode de mesure du sable de Noble Energy. À chaque séparateur, Hawkins commence par stabiliser l'une des deux caméras FLIR GFx320 sur un monopode. Il la positionne de manière à voir les côtés du réservoir du séparateur et passe en mode manuel pour établir des points de consigne. Le bain de pétrole du séparateur oscille en général entre 32 et 37,7 °C (90 et 100 °F). La pile de sable affiche une température environ équivalente à la température ambiante. Donc si la température ambiante est de 15,5 °C (60 °F), on observera un delta de -1 à 4,4 °C (30 à 40 °F) entre le bain de pétrole et la pile de sable. Le sable s'accumule en général au fond du réservoir, tandis que la paraffine est plus dispersée et se trouve plutôt au milieu du réservoir. La paraffine colle aux côtés du réservoir, contrairement au sable. Pour suivre l'état de chaque séparateur, Hawkins a créé un programme de surveillance basé sur le numéro de série de chaque séparateur. Quand une pile de sable est détectée, le séparateur est ajouté au programme de surveillance. Les séparateurs des puits récemment fracturés sont étroitement surveillés car l'essentiel du sable remonte après la fracturation initiale.
La sécurité intrinsèque, un impératif absolu
Pour les séparateurs du programme de surveillance, Noble Energy compare des images mensuelles pour déterminer à quelle vitesse le sable s'accumule et à quel moment un nettoyage devient nécessaire. Deux éléments clés assurent le bon fonctionnement du programme. Tout d'abord, les caméras doivent être intrinsèquement sûres en raison des risques d'incendie à proximité des séparateurs. Les caméras intrinsèquement sûres sont conçues pour maintenir leur énergie (électrique et thermique) à des niveaux non incendiaires, de manière à ce qu'un court-circuit ou une panne ne provoque pas d'étincelle, un aspect essentiel dans les atmosphères explosives. La GFx320 intrinsèquement sûre permet à Hawkins et son équipe de s'approcher de chaque séparateur, de l'inspecter sous plusieurs angles et d'éviter les reflets du soleil, qui peuvent chauffer la surface du séparateur. Selon Hawkins, « Avant la caméra intrinsèquement sûre, je ne pouvais parfois prendre qu'une photo de l'avant d'un réservoir, parce que je ne pouvais pas m'approcher à moins d'un mètre cinquante du séparateur adjacent. »
Comme on le voit dans la photographie aérienne, des rangées de séparateurs étroitement alignés limitent l'accès à chaque réservoir. « Une caméra intrinsèquement sûre fait une différence considérable pour l'exécution de ce programme, » explique Hess. « Nous pouvons désormais inspecter des recoins qui étaient jusqu'ici inaccessibles. » Ensuite, les images doivent être similaires, ce qui signifie que le même opérateur doit capturer puis manipuler ou affiner les images. « Nous essayons toujours d'obtenir des images similaires pour établir des tendances. Ainsi, quand on les compare les unes aux autres on détecte plus facilement les différences. Si vous demandez à des personnes différentes de faire les relevés, vous verrez que chaque regard produit des images différentes », commente Hawkins. Hawkins et ses collègues spécialement formés à cette méthode ont évalué plus de 7 000 séparateurs en 2017. Selon Hess : « Landon possède ce regard aiguisé, et il a formé d'autres techniciens à la méthode qu'il a mise au point. Il est incontestablement le fer de lance de tout le programme. » Parmi les plus de 7 000 séparateurs inspectés, 300 ont été arrêtés pour que le sable puisse en être retiré.
Atteindre 100 % de précision
Hawkins et son équipe utilisent deux caméras infrarouges FLIR GFx320 intrinsèquement sûres pour optimiser le programme de maintenance préventive de Noble Energy concernant les séparateurs. Si la réussite du programme repose en grande partie sur l'expérience acquise avec la caméra, Hawkins continue d'améliorer et de documenter sa méthode pour la rendre plus accessible aux autres techniciens. En attendant, le programme de surveillance a déjà produit des dividendes majeurs en identifiant, en moins d'un an, 300 réservoirs présentant des accumulations de sable suffisantes pour mettre en danger les fragiles tubes chauffants. Il n'y a aucun moyen de savoir si ces 300 réservoirs seraient tombés en panne sans ce nettoyage. Même si la surveillance effectuée à l'aide de la GFx320 n'a permis d'éviter qu'une seule panne, elle aura évité 100 000 $ de frais de remplacement du réservoir, sans compter les heures-hommes perdues par l'équipe de maintenance. La preuve est dans le sable. « Je travaille en étroite collaboration avec l'équipe de maintenance qui fait tout le travail de nettoyage et selon eux nous avons un taux de réussite de 100 %. Chaque séparateur que nous avons signalé pour nettoyage en utilisant cette méthode présentait effectivement une accumulation importante de sable.